5 Ways To Be Efficient At Order Picking
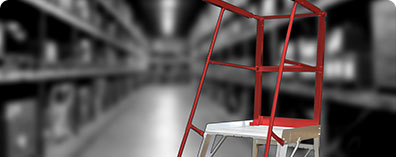


Order picking is the process of locating and extracting products to fill customer orders. It is one of many steps involved in order processing, and is a vital activity in any warehouse. Considering that stock picking has a direct impact on customer satisfaction, reduced labour costs and warehouse efficiency, it is imperative that you are constantly reflecting on how you can make warehouse picking as efficient as possible. In doing so, you are able to reduce the amount of human error and unproductiveness that can oftentimes be present in order picking operations. Thus below are 5 approaches you can employ to increase productivity in your warehouse.
Try out different order picking methods
You can try a myriad of different order picking methods in your warehouse, including zone picking, batch picking and wave picking. There is no one right method, however it is important to choose what suits your warehouse’s needs.
Zone picking is a method where order pickers are assigned a specific zone within the warehouse, and they are just responsible for picking the SKUs in their designated zone. This method is ideal for situations in which several orders come through at the same time. While there is generally less interference with other order pickers blocking aisles, this method is not ideal in situations where customer orders do not come through on a frequent or regular basis. Equip2Go’s TS2B Order Picking Trolley is great for zone picking with its two shelves and high durability.
Batch picking is when an order picker retrieves multiple orders at the same time, minimising repeat trips to the same location. This is particularly convenient when there are multiple orders with the same SKU. While it is time-saving, it can result in an overcrowding of order pickers getting in each others’ zones. You can use our HS808LI Quad Deck Service Trolley Cart for batch picking as it has 4 shelves to place items on.
Wave picking is when all orders from all zones are picked at the same time and are later sorted and consolidated into individual shipments. Although this can make picking and shipping operations a faster process, this method risks the improper sorting of products. Equip2Go’s TS4B Stock Picking Trolley is perfect for batch picking as it contains 4 separate compartments on the top as well as space for large products on the bottom.
Other methods of stock picking include cluster picking and discreet order picking (also known as piece picking). You can likewise do a variation of methods that include elements from each other, such as zone-batch picking or zone-wave picking. It is important to choose the right method for your warehouse’s needs.
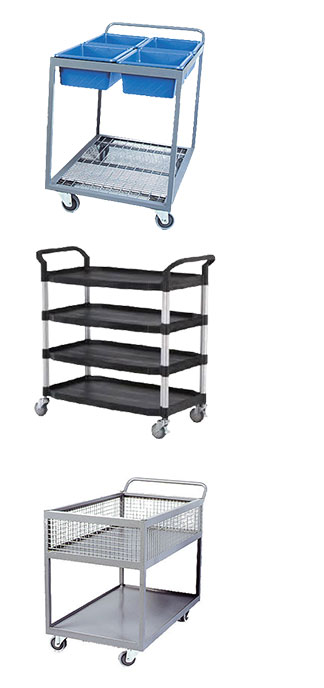
Position products in your warehouse in a practical and time-saving way
The placement of products within your warehouse can drastically affect the amount of time it takes to retrieve them. By grouping together and placing popular and high-sales items close to shipping trucks (and placing less popular items farther away), the speed and efficiency at which orders are picked is greatly improved. Additionally, since it takes more time to reach higher levels, keeping high-sales products at ground/lower levels further increases productivity as you are able to access them easily. No matter the level you need to reach your products, Equip2Go has Monstar Order Picker Ladders ranging from 2 steps to 6 steps to suit your needs.
Overall, being mindful of the arrangement of your products in a warehouse reduces the amount of movement required, as well as potential fatigue and misjudgement in workers from too much walking around. This not only increases productivity and efficiency, but also allows for smoother operations within your warehouse.
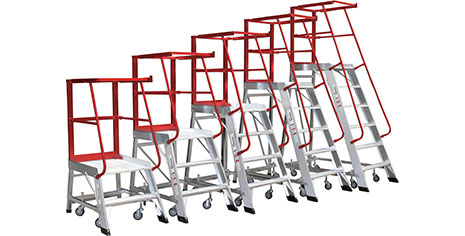
Limit the amount of people who have contact with the order
It is easier to prevent errors and inaccuracies during the inventory picking and processing rather than having to face the consequences afterwards. In general, order pickers should be the only ones who have contact with products before they go onto a shipping truck. This lowers the chance of human error and potential misunderstandings when relaying information to another worker on where an order needs to go. By eliminating this unnecessary extra step, order pickers can remain focused on the correct delivery of products to shipping trucks, and the risk of having to repack, reship or recheck products is significantly lowered.
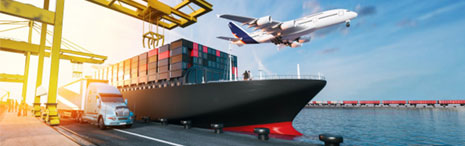
Check and replenish inventory when needed
Consistently maintaining a stocked inventory ensures that supply never runs out and order pickers are able to retrieve products without any issues. There are many computer applications that you can use to help track the status of your inventory and that allow you to re-stock before it becomes depleted. This is necessary in smoothly running a warehouse.
Invest in order picking training
Training workers in using the most suitable and efficient order preparation methods has many benefits for your warehouse operations. Not only does effective training provide workers with the necessary knowledge and skills, it also saves time, money and effort in the long run. Additionally, workers are able to learn how to function well within a team to achieve a desired outcome and ultimately enhance warehouse productivity and customer satisfaction. Training can really make the difference between mediocre and effective warehouse management.
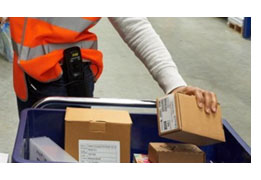
A smooth and steady order picking system is the key to success in material handling and warehouse equipment industries. The effective measures listed above can not only boost time-efficiency, productivity and customer satisfaction, but they also play a significant role in the economical growth of your company. Moreover, Equip2Go has a broad selection of industrial order picking trolleys and ladders that can further improve efficiency in your warehouse. Check out our website for more information.